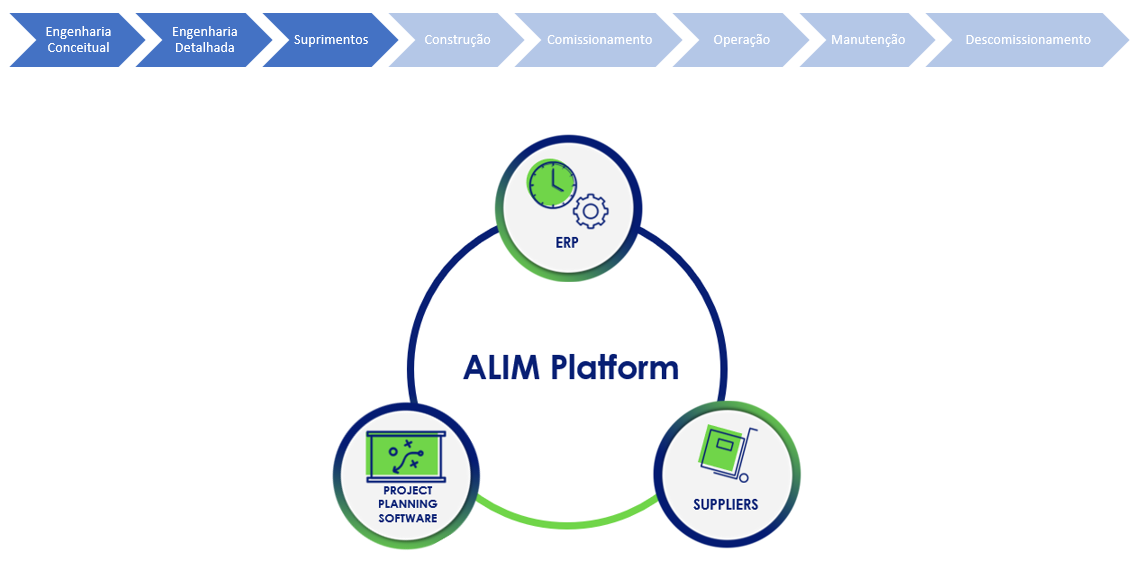
Neste artigo, tentarei explicar por que e como uma abordagem de fluxo de dados entre os principais sistemas durante o ciclo de vida das plantas industriais é muito mais eficaz do que um processo de entrega baseado em documentos entre as fases do projeto. Falamos anteriormente sobre as várias estruturas de informações que precisam estar em vigor no mesmo ciclo de vida. Se você estiver interessado, a lista de artigos é encontrada no final deste artigo.
Durante as fases de projeto conceitual e engenharia, as diferentes disciplinas técnicas que desenvolvem os projetos das plantas industriais e dos produtos (equipamentos) assim como as respectivas ferramentas (softwares) utilizadas desempenham um papel importante, pois são sistemas responsáveis pela alimentação da plataforma ALIM – Asset Lifecycle Information Management. Todas as informações provenientes dessas ferramentas precisam ser padronizadas, consolidadas, gerenciadas e colocadas sob um rígido processo de gestão de mudanças. A plataforma ALIM também desempenha um papel importante para documentar as linhas de base técnicas da planta industrial, como conforme projetado, conforme construído, conforme comissionado e como mantido. Veja a figura 1.
Ao passar para a fase de suprimentos, uma enorme quantidade de informações precisa fluir para o sistema ERP para a aquisição de tudo o que é necessário para a construção da planta. As primeiras informações que devem ser transferidas são os projetos aprovados e liberados pela engenharia, portanto, listas de materiais e equipamentos especificados a aprovados. Este é o domínio tradicional do Gerenciamento do Ciclo de Vida de Projetos. As chamadas LM’s (listas de materiais) ou BOM’s (bill of materials) geradas durante a fase de projeto e publicadas dizem que, do ponto de vista da engenharia, tudo está pronto para a fabricação, aquisição ou montagem e o ERP pode iniciar o processo de aquisição das peças, equipamentos e materiais para início da fabricação ou montagem. Dependendo do nível da engenharia da planta, pode haver uma quantidade extremamente grande de itens ou apenas peças individuais representando componentes ou peças padrões.
As próximas informações que precisam ser transferidas para o ERP são informações de TAG’s especificadas e aprovadas pela engenharia, onde a TAG está conectada a uma peça. Um exemplo típico seria um sistema de tubulação que é desenvolvido e aprovado com, digamos, 8 TAG’s de bombas e os requisitos individuais de cada bomba presentes no sistema podem ser atendidos por um item genérico de um fabricante. Isso significa que no sistema ALIM existem 8 objetos tagueados como bombas aprovadas pela engenharia todos os TAG’s estão conectados ao mesmo item genérico. Isto constitui uma demanda específica validada pelo projeto por 8 bombas. Nesse estágio, uma linha de base “As-Designed” pode ser criada na plataforma ALIM para esse sistema específico.
Estas informações devem ser transferidas para o ERP de forma automática, onde uma requisição de compras é grada para suprir uma demanda de 8 bombas e gerenciar a logística em torno deste fornecimento. No entanto, do ponto de vista do planejamento e execução do projeto, pode-se identificar que, de acordo com o planejamento do projeto, vários outros sistemas estão programados para serem finalizados pela engenharia em breve, o que geraria um pedido 50 bombas em vez de 8. Depois uma análise junto às demais partes interessadas afetadas, pode ser que seja decidiu adiar o pedido para que seja possível a colocação de um pedido maior junto ao fornecedor, doando ao comprador um poder maior de negociação.
Como o pedido de compras é feito juntamente com as informações relativas a cada requisito específico de cada TAG, é necessário fazer a preparação para o recebimento de mercadorias, armazenamento intermediário e ordens de serviço para instalação. Isso normalmente é feito pelo sistema ALIM – Asset Lifecycle Information Management, que conhece cada TAG e seus requisitos, locais físicos de instalação de cada bomba e a respectiva definição de peça correspondente o ativo físico recebido. Todas essas informações já estão no sistema ALIM desde a finalização da respectiva engenharia. À medida que os ativos físicos são recebidos, cada uma das nossas 50 bombas agora precisa ser inspecionada, registrada no sistema ALIM (módulo de WMS – Warehouse Management System) juntamente com as informações fornecidas pelo fabricante e associadas à definição de peça comum. Assim que as bombas estiverem programadas para instalação, cada ativo físico entregue será identificado como agora instalado para cumprir uma função dedicada na planta (item tagueado).
Nesse estágio, as informações sobre o ativo físico e suas relações com o TAG, a localização física e a parte correspondente já se encontram consolidadas na Plataforma ALIM. Esta etapa é crucial quando se necessita a comparação entre o “As-Designed” com o “As-Built”.
A próxima etapa será a integração da Plataforma ALIM com sistema de Controle/Automação e Segurança estando estes cientes dos ativos instalados. Isso estará entre os tópicos do próximo artigo.